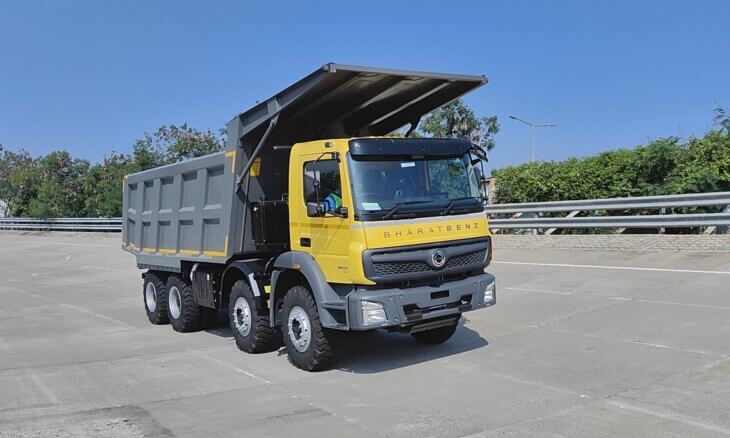
Daimler India Commercial Vehicles (DICV) has inaugurated a cutting-edge Mechatronics Lab at its Oragadam facility. The new lab is set to revolutionise the efficiency of software architecture verification and validation for DICV’s trucks and buses, promising cost savings of 70-80 per cent compared to traditional methods.
The lab leverages agile methodologies to quickly identify and resolve software bugs through a closed-loop feedback system, drastically reducing the time required for testing and verification. Processes that previously took weeks or months can now be completed within days, enhancing the overall quality and efficacy of DICV’s testing processes.
The Mechatronics Lab is pivotal in ensuring that Daimler Truck products manufactured at DICV not only meet current safety standards but also stay ahead of future global safety regulations. It verifies and validates software feature functionality, aligning with DICV’s commitment to technological leadership in the commercial vehicle sector.
Pradeep Kumar Thimmaiyan, President – Product Engineering & Chief Technology Officer, DICV, commented on the lab’s inauguration: “Our new Mechatronics Lab signals a transformative phase in our Research and Development operations, ushering us into an era that underscores enhanced agility and breakthrough innovations. Beyond validation, our Mechatronics Lab stands as a hub for innovation, positioning us uniquely on the global stage. Already, the lab is the core of our future electrical and electronic architectures. The DICV Mechatronics Lab complements the company’s long-term vision, positioning it at the forefront of technological advancements in the commercial vehicle sector. It underscores our commitment to ‘Make and Develop in India, for India and the World’, embodying our vision to not only cater to domestic needs but also to set new benchmarks internationally.”
Dilip Shrivastava, Head – Mechatronics and Software Technology, DICV, highlighted the lab’s capabilities: “Our Lab can verify and validate around 300 features, encompassing over a thousand signals within 10 days, and can verify 600 fault codes in a developing product in just a few weeks, which otherwise would have taken months. Our aim is to ensure our software architecture gets verified and validated before it gets embedded in our trucks and buses as early identification of software bugs which saves enormous developmental cost. Keeping our long-term vision in mind we are bringing such efficiencies that can accelerate product development cycles for which our Mechatronics Lab will play a lead role. By establishing the lab, evaluation of diverse vehicle architectures has become seamless, eliminating the need for multiple test vehicles while enhancing the overall efficiency.”
The Mechatronics Lab also features advanced infrastructure, including a flashing station for pre-production verification of all ECUs, ensuring hardware and software compatibility, and an ADAS setup that reproduces on-road data in the lab for initial software modifications. These capabilities significantly reduce vehicle dependency and enhance the safety and efficiency of DICV’s product development processes.
The lab’s ability to simulate rare fault cases, difficult to replicate in real-world conditions, ensures comprehensive verification and validation, ultimately leading to safer and more reliable commercial vehicles.