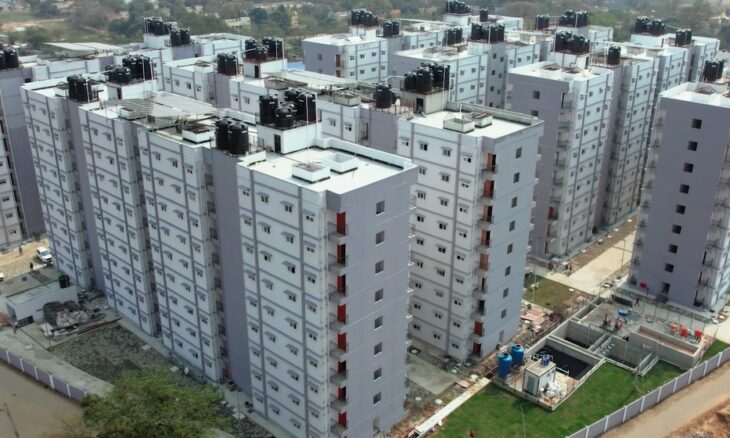
Magicrete has announced the completion of India’s inaugural mass housing project in Ranchi, employing the 3D Modular Precast Construction System. This achievement signifies a significant stride towards addressing the escalating housing demands in India with celerity, sustainability, and quality.
The project, featuring 1,008 dwelling units, has demonstrated cost equivalence with traditional construction methods while substantially diminishing construction duration by up to 40 per cent. This development not only enhances housing accessibility but also highlights the potential of precast concrete technology to revolutionise India’s construction industry.
Sourabh Bansal, Managing Director, Magicrete, stated, “Magicrete remains dedicated to fostering innovation and sustainable development within the construction sector, thereby illuminating a promising path for India’s built environment.”
“I am immensely proud of our team’s dedication in bringing India’s first mass housing project in Ranchi to fruition,” Bansal added. “This initiative not only addresses the pressing housing needs of the urban poor but also showcases the transformative potential of precast concrete technology in providing sustainable, resilient, and affordable housing solutions.”
The project aims to offer dignified living to the urban poor, benefiting 1,008 families with cost-effective and robust homes requiring minimal maintenance. These disaster-resilient residences will furnish a healthy and environmentally-friendly habitat for improved living standards. Additionally, the project ensures convenient access to public transport, healthcare, education, and livelihood facilities, thereby empowering communities and fostering inclusive development.
“Magicrete’s expertise in leveraging volumetric technology further augmented the efficiency and quality of the housing units in the project,” Bansal noted. “By minimising elements and joints, ensuring a waterproof structure, and expediting production and erection processes, the project exemplifies the potential of precast concrete technology in delivering superior housing solutions.”
Despite initial challenges concerning land acquisition, the project was completed within 18 months, showcasing Magicrete’s commitment to punctual delivery and excellence in execution.
In terms of materials, the project utilised Portland Slag Cement with a high percentage of Ground Granulated Blast Furnace Slag (GGBFS), resulting in a reduction of the carbon footprint by approximately 60 per cent. Additionally, M-sand replaced traditional river sand in concrete production, contributing to sustainability efforts. The incorporation of rooftop solar panels, rainwater harvesting systems, solar street lights, and a sewage treatment plant further underscored the project’s commitment to environmental responsibility.